DACHSER South Africa expands coastal cross-docking facilities
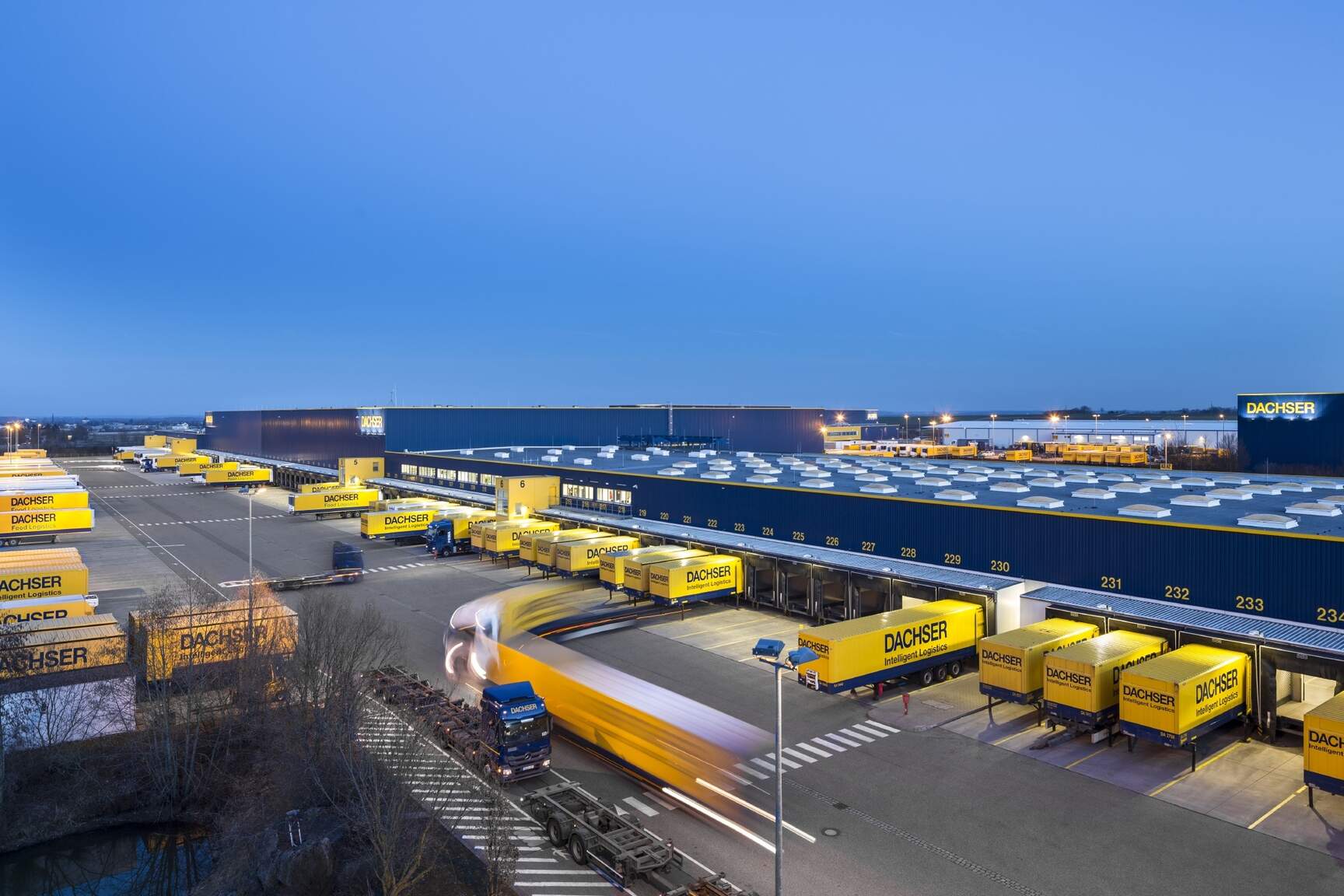
Cross-docking, where inbound cargo is unloaded from an incoming container, sorted and then loaded directly to outbound carriers, is an important logistics strategy that keeps supply chains moving in a productive, effective manner. Logistics leader, DACHSER South Africa, has recently expanded its Durban operations to a new 3600sqm warehouse in Pinetown, Durban.
“The new off-loading and loading bays have increased our capacity to handle a number of containers at a time, enabling us to offer excellent turn-around times,” says Detlev Duve, DACHSER South Africa, Managing Director, “The facility provides a dedicated central site for products to be sorted for delivery to multiple destinations in the most productive way, saving costs. Ultimately, our customers benefit from a more efficient supply chain.”
Deidre Smith, DACHSER Sea Freight Imports Manager, says, “We’re able to consolidate shipments, or even break down larger shipments into smaller loads, for easier delivery. Storage and handling costs can be reduced as products spend less time in the warehouse. Cargo also typically reaches its final destination faster, giving our customers a competitive edge.”
Further to a spacious, well-equipped warehouse, Smith says that experienced staff and effective planning are the foundations of a successful operation. “Skilled staff are vital to the operation and management of the warehouse. From expert inventory control using Warehouse Management Systems, through to our material handling equipment operators and cargo handling teams, we ensure that all our staff are well-trained and clear on the different goods and requirements of our customers.”
Smith explains that the goods that are most conducive to cross-docking are those that are in steady demand, usually higher volume, fast-moving products scheduled in regular dispatches to pre-planned destinations. DACHSER also has the experience to handle large or complex items. “Of course, the preferred cargo to handle is stackable, palletised cargo that fits neatly into racks can be easily transported, but we’ve become experts in handling the odd and awkward cargo too. Taking care of customers cargo and avoiding damages is our top priority, and our Durban handling team has the experience to load the trucks safely and correctly. We also ensure that the appropriate handling equipment is available when off-loading a container and manoeuvring the cargo around the warehouse.”
The DACHSER team handles both Pre-Distribution, where goods are unloaded and despatched according to set distribution instructions, and Post-Distribution processes, usually for retailers, which entails flexible picking and packing according to demand, based on in-store inventory, sales forecasts and trends.
Duve says it is also essential to partner with reputable transporters that offer a regular and reliable service to move the goods from warehouse to customer door.
“With all the right foundations in place, cross-docking has become part of the seamless supply chain solution DACHSER South Africa offers to our customers, which further includes contract logistics, value-added warehousing, customs clearance and customs warehousing services,” says Duve.
About DACHSER:
A family-owned company headquartered in Kempten, Germany, DACHSER is a leading supplier of logistics services worldwide.
DACHSER offers comprehensive transport logistics, warehousing, and customer-specific services in two business fields: DACHSER Air & Sea Logistics and DACHSER Road Logistics. The latter consists of two business lines: DACHSER European Logistics and DACHSER Food Logistics. Comprehensive contract-logistics services and industry-specific solutions round out the company’s offerings. A seamless shipping network—both in Europe and overseas—and fully integrated IT systems ensure intelligent logistics solutions worldwide.
Thanks to some 30,995 employees at 393 locations all over the globe, DACHSER generated revenue of 5.66 billion euros in 2019. That same year, the logistics provider handled a total of 80.6 million shipments weighing 41. million metric tons. Country organizations represent DACHSER in 44 countries.