DACHSER South Africa celebrates 40 years as the gateway to Africa
DACHSER South Africa (SA) celebrates 40 years of being in business this November. When global logistics provider DACHSER acquired Jonen Freight, owned by the Duve family, in 2011, the newly minted DACHSER SA strengthened its global network, bringing over 30 years of established expertise in Africa to the company. Under the leadership of Managing Director Detlev Duve, DACHSER SA has further established itself as the gateway to Africa, dealing with diverse logistics needs across the various trade lanes and growing the team and the business in the face of a very challenging economic environment.
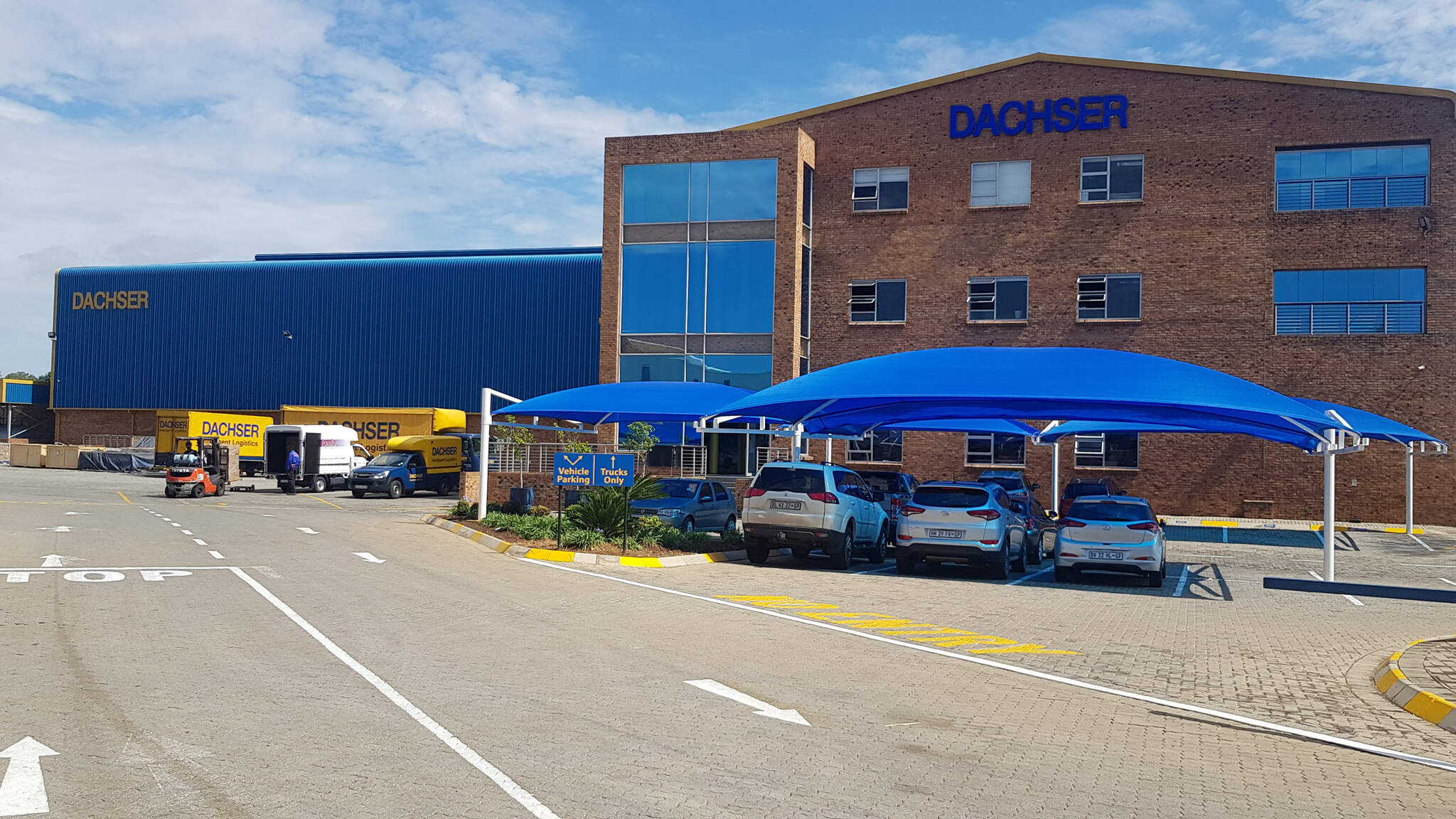
Recalibrating medical equipment for delivery all over Africa, moving mega-mining components to remote locations or sending fresh food products to Zambia and Zimbabwe by road freight or Mauritius, Madagascar and Mayotte by sea is all in a day’s work for the DACHSER SA teams. “We are specialists in moving products through Africa, from oversized capital equipment to urgent samples to general cargo,” says Duve.
Our colleagues across the world trust our local teams to complete the job into Africa as we have an in-depth understanding of the complexities of supply chain management and logistics in the African continent, such as customs, inspections, infrastructure challenges and delays at border crossings.
Detlev Duve, Managing Director DACHSER South AfricaDACHSER SA further offers value-added warehousing solutions from its large warehousing space in Johannesburg. Globally, DACHSER now has more employees than at any other point in its history: some 30.603 people around the world are employed by the family-owned company based in Kempten, Germany. DACHSER SA is home to 240 of these employees working across four branches, involved at any given time in connecting the flow of commodities, information, and transport companies with each other. Over 200 jobs have been created and the company has invested heavily in skills development, taking on 15 interns per year and employing many of them.
40 years of operating in Africa
“We’re proud of the strong relationships we’ve built, the experience we’ve gained and the milestones we’ve achieved over 40 years of operating in Africa. It’s incredible that a family business started by my father, Hartmut Duve, now adds value to the incredible global network DACHSER offers – itself also a family business. We’ll strive to continue the legacy as we play a vital role in helping clients harness business opportunities in Africa.”